Why isn't there any 9.5 digit multimeter or higher?different current readings with a multimeter between the 200 mA and the 10 A slotsWhy do multimeters show values at the lower parts of a given range the way they do?What to look for in a multimeter?Why would you use a non-contact voltage detector if you have a multimeter?Why won't this bulb light when I put the multimeter in series?Why isn't Ohm's law working for this simple circuit?Why isn't there a ground on a 7-Segment display?Why are readings from multimeter leads are too high?Accuracy error of ammeter from specification : is it really just a constant offset?Is a multimeter with 1,200,000 counts actually a 6½ digit multimeter?
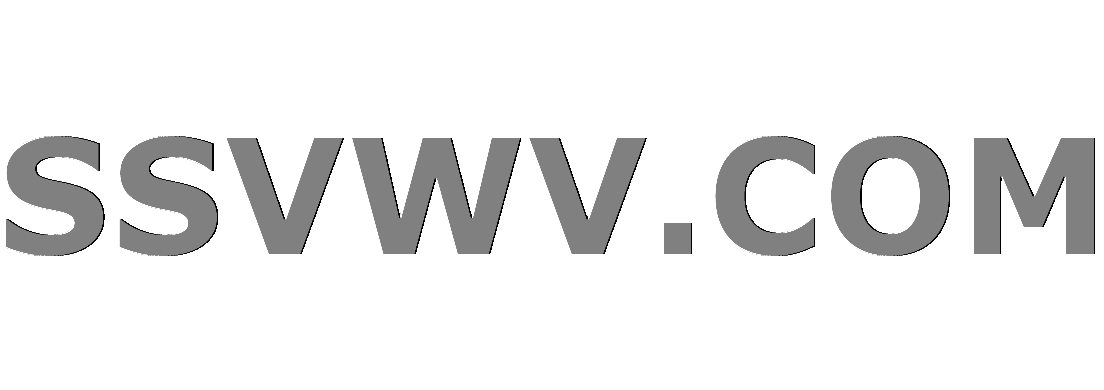
Multi tool use
What can make Linux so unresponsive?
Should I take out a personal loan to pay off credit card debt?
Our group keeps dying during the Lost Mine of Phandelver campaign. What are we doing wrong?
Differentiability of operator norm
Does this smartphone photo show Mars just below the Sun?
Making pause in a diagram
Why does putting a dot after the URL remove login information?
Are children a reason to be rejected for a job?
Was Richard I's imprisonment by Leopold of Austria justified?
Validation and verification of mathematical models
What are the examples (applications) of the MIPs in which the objective function has nonzero coefficients for only continuous variables?
Does the Voyager team use a wrapper (Fortran(77?) to Python) to transmit current commands?
What is the purpose of this mount on the upper suspension arm?
Probably terminated or laid off soon; confront or not?
What does VB stand for?
Is there a drawback to Flail Snail's Shell defense?
Does a 4 bladed prop have almost twice the thrust of a 2 bladed prop?
ESTA declined to the US
What could prevent players from leaving an island?
How can I refer to something in a book?
How do these cubesats' whip antennas work?
Why should I "believe in" weak solutions to PDEs?
Will a paper be retracted if a flaw in released software code invalidates its central idea?
What word best describes someone who likes to do everything on his own?
Why isn't there any 9.5 digit multimeter or higher?
different current readings with a multimeter between the 200 mA and the 10 A slotsWhy do multimeters show values at the lower parts of a given range the way they do?What to look for in a multimeter?Why would you use a non-contact voltage detector if you have a multimeter?Why won't this bulb light when I put the multimeter in series?Why isn't Ohm's law working for this simple circuit?Why isn't there a ground on a 7-Segment display?Why are readings from multimeter leads are too high?Accuracy error of ammeter from specification : is it really just a constant offset?Is a multimeter with 1,200,000 counts actually a 6½ digit multimeter?
.everyoneloves__top-leaderboard:empty,.everyoneloves__mid-leaderboard:empty,.everyoneloves__bot-mid-leaderboard:empty margin-bottom:0;
$begingroup$
Why can't you buy a 91⁄2-digit multimeter?
Isn't there any need for it? Is a 81⁄2-digit multimeter the latest high end you can buy? I have tried Keysight, Keithley, and Fluke, but there is nothing higher than 81⁄2 digits.
voltage multimeter precision resolution
$endgroup$
|
show 11 more comments
$begingroup$
Why can't you buy a 91⁄2-digit multimeter?
Isn't there any need for it? Is a 81⁄2-digit multimeter the latest high end you can buy? I have tried Keysight, Keithley, and Fluke, but there is nothing higher than 81⁄2 digits.
voltage multimeter precision resolution
$endgroup$
10
$begingroup$
What is your goal?
$endgroup$
– Chris Stratton
Jul 27 at 22:04
38
$begingroup$
You'd need a 10.5 digit meter to calibrate it.
$endgroup$
– Transistor
Jul 27 at 22:09
11
$begingroup$
What's the true accuracy of even that 8.5 digit DMM? Probably not 1 part in 100 million...
$endgroup$
– Brian Drummond
Jul 27 at 23:03
12
$begingroup$
Check NIST. I think you'll find that accuracy of their best Josephson Junction devices is on the order of a some parts in $10^10$. So, roughly speaking, about 9.5 digits. And that's under optimal conditions. The equipment used to provide such a standard costs about $300k each and will probably require a PhD to operate well. There's a recent 2018 paper on the topic, "Impact of the latest generation of Josephson voltage standards in ac and dc electric metrology" by Rüfenacht, et al. DOI: 10.1088/1681-7575/aad41a. You can buy a voltage standard that is 9.5 digits. Not a multimeter, though.
$endgroup$
– jonk
Jul 28 at 0:46
7
$begingroup$
Every potential customer must answer for themselves the following questions: What are you trying to measure? Why do you require or want an accuracy of around a part in 1000 million? How would you calibrate it? What is your budget?
$endgroup$
– Russell McMahon
Jul 28 at 2:54
|
show 11 more comments
$begingroup$
Why can't you buy a 91⁄2-digit multimeter?
Isn't there any need for it? Is a 81⁄2-digit multimeter the latest high end you can buy? I have tried Keysight, Keithley, and Fluke, but there is nothing higher than 81⁄2 digits.
voltage multimeter precision resolution
$endgroup$
Why can't you buy a 91⁄2-digit multimeter?
Isn't there any need for it? Is a 81⁄2-digit multimeter the latest high end you can buy? I have tried Keysight, Keithley, and Fluke, but there is nothing higher than 81⁄2 digits.
voltage multimeter precision resolution
voltage multimeter precision resolution
edited Jul 28 at 12:45
Peter Mortensen
1,5983 gold badges14 silver badges22 bronze badges
1,5983 gold badges14 silver badges22 bronze badges
asked Jul 27 at 21:55
voltage_dropvoltage_drop
771 silver badge3 bronze badges
771 silver badge3 bronze badges
10
$begingroup$
What is your goal?
$endgroup$
– Chris Stratton
Jul 27 at 22:04
38
$begingroup$
You'd need a 10.5 digit meter to calibrate it.
$endgroup$
– Transistor
Jul 27 at 22:09
11
$begingroup$
What's the true accuracy of even that 8.5 digit DMM? Probably not 1 part in 100 million...
$endgroup$
– Brian Drummond
Jul 27 at 23:03
12
$begingroup$
Check NIST. I think you'll find that accuracy of their best Josephson Junction devices is on the order of a some parts in $10^10$. So, roughly speaking, about 9.5 digits. And that's under optimal conditions. The equipment used to provide such a standard costs about $300k each and will probably require a PhD to operate well. There's a recent 2018 paper on the topic, "Impact of the latest generation of Josephson voltage standards in ac and dc electric metrology" by Rüfenacht, et al. DOI: 10.1088/1681-7575/aad41a. You can buy a voltage standard that is 9.5 digits. Not a multimeter, though.
$endgroup$
– jonk
Jul 28 at 0:46
7
$begingroup$
Every potential customer must answer for themselves the following questions: What are you trying to measure? Why do you require or want an accuracy of around a part in 1000 million? How would you calibrate it? What is your budget?
$endgroup$
– Russell McMahon
Jul 28 at 2:54
|
show 11 more comments
10
$begingroup$
What is your goal?
$endgroup$
– Chris Stratton
Jul 27 at 22:04
38
$begingroup$
You'd need a 10.5 digit meter to calibrate it.
$endgroup$
– Transistor
Jul 27 at 22:09
11
$begingroup$
What's the true accuracy of even that 8.5 digit DMM? Probably not 1 part in 100 million...
$endgroup$
– Brian Drummond
Jul 27 at 23:03
12
$begingroup$
Check NIST. I think you'll find that accuracy of their best Josephson Junction devices is on the order of a some parts in $10^10$. So, roughly speaking, about 9.5 digits. And that's under optimal conditions. The equipment used to provide such a standard costs about $300k each and will probably require a PhD to operate well. There's a recent 2018 paper on the topic, "Impact of the latest generation of Josephson voltage standards in ac and dc electric metrology" by Rüfenacht, et al. DOI: 10.1088/1681-7575/aad41a. You can buy a voltage standard that is 9.5 digits. Not a multimeter, though.
$endgroup$
– jonk
Jul 28 at 0:46
7
$begingroup$
Every potential customer must answer for themselves the following questions: What are you trying to measure? Why do you require or want an accuracy of around a part in 1000 million? How would you calibrate it? What is your budget?
$endgroup$
– Russell McMahon
Jul 28 at 2:54
10
10
$begingroup$
What is your goal?
$endgroup$
– Chris Stratton
Jul 27 at 22:04
$begingroup$
What is your goal?
$endgroup$
– Chris Stratton
Jul 27 at 22:04
38
38
$begingroup$
You'd need a 10.5 digit meter to calibrate it.
$endgroup$
– Transistor
Jul 27 at 22:09
$begingroup$
You'd need a 10.5 digit meter to calibrate it.
$endgroup$
– Transistor
Jul 27 at 22:09
11
11
$begingroup$
What's the true accuracy of even that 8.5 digit DMM? Probably not 1 part in 100 million...
$endgroup$
– Brian Drummond
Jul 27 at 23:03
$begingroup$
What's the true accuracy of even that 8.5 digit DMM? Probably not 1 part in 100 million...
$endgroup$
– Brian Drummond
Jul 27 at 23:03
12
12
$begingroup$
Check NIST. I think you'll find that accuracy of their best Josephson Junction devices is on the order of a some parts in $10^10$. So, roughly speaking, about 9.5 digits. And that's under optimal conditions. The equipment used to provide such a standard costs about $300k each and will probably require a PhD to operate well. There's a recent 2018 paper on the topic, "Impact of the latest generation of Josephson voltage standards in ac and dc electric metrology" by Rüfenacht, et al. DOI: 10.1088/1681-7575/aad41a. You can buy a voltage standard that is 9.5 digits. Not a multimeter, though.
$endgroup$
– jonk
Jul 28 at 0:46
$begingroup$
Check NIST. I think you'll find that accuracy of their best Josephson Junction devices is on the order of a some parts in $10^10$. So, roughly speaking, about 9.5 digits. And that's under optimal conditions. The equipment used to provide such a standard costs about $300k each and will probably require a PhD to operate well. There's a recent 2018 paper on the topic, "Impact of the latest generation of Josephson voltage standards in ac and dc electric metrology" by Rüfenacht, et al. DOI: 10.1088/1681-7575/aad41a. You can buy a voltage standard that is 9.5 digits. Not a multimeter, though.
$endgroup$
– jonk
Jul 28 at 0:46
7
7
$begingroup$
Every potential customer must answer for themselves the following questions: What are you trying to measure? Why do you require or want an accuracy of around a part in 1000 million? How would you calibrate it? What is your budget?
$endgroup$
– Russell McMahon
Jul 28 at 2:54
$begingroup$
Every potential customer must answer for themselves the following questions: What are you trying to measure? Why do you require or want an accuracy of around a part in 1000 million? How would you calibrate it? What is your budget?
$endgroup$
– Russell McMahon
Jul 28 at 2:54
|
show 11 more comments
5 Answers
5
active
oldest
votes
$begingroup$
Four reasons:
- Because modern meters have an autoranging function.
- Because the dynamic range of the analog system would not support 91⁄2 digits, with a range of 1 V the noise floor would be in the nanovolts (you can't get lower than nanovolts because of thermal noise, without significant cooling of what your measuring to reduce the thermal noise temperature), and all of the digits below the 9th would be noisy.
- ADCs usually have a 5 V range, and even with a 24-bit ADC, you'll have roughly 60 nV per bit which restricts the resolution of the last digits.
- On a 6.5 digit meters that are commonly used, for most measurements around a normal lab have noise in the uV range. And the last digits are commonly noisy on a 6.5 digit meter. One more digit might be nice for some applications, 3 more digits would be frivolous.
Even nanovolt meters don't have 91⁄2 digits.
For most measurements 6 (or so) digits will suffice because great care must be taken to lower the noise floor below 1 μV.
Here is a cool scale that also illustrates the point:
Source: Understanding and Applying Voltage References
It's difficult to obtain gains larger than 140dB with an analog subsystem, and about that point your also limited on resolution. Gaining doesn't help because of the noise inherent in all analog electronics, you gain up the signal, you also gain up the noise.
The marketing departments can ask for more digits, but it's not going to help engineers.
$endgroup$
9
$begingroup$
Autoranging with relays can play havoc with sensitive experiments, so in the physics lab I work in we normally turn it off. Thus for one experiment we need a 6.5 digit multimeter to get 3.5 digits at the start and not saturate the photodiode at the end.
$endgroup$
– Chris H
Jul 28 at 18:20
$begingroup$
You can take your signal, filter it, then amplify it with a gain of 2 or more, and measure three digits there (then divide by your gain for your measurement). This is usually what is done when you need more precision with a 10-bits ADC (like the one you find on most microcontrollers) for pretty much a couple of cents in parts.
$endgroup$
– Drunken Code Monkey
Jul 30 at 2:58
2
$begingroup$
@DrunkenCodeMonkey Yes, this works for 10-bits, 10bits is equivalent to 3.5digits. There is no way to increase the SNR for the frequency's you are measuring. Filtering will reduce the overall pk-pk noise, but will do nothing for sensor noise. If the noise per given frequency is 10nv/Hz at the input then there is no amount of gaining or filtering to get better SNR. The other problem is every time you add a filter or analog stage, you increase the noise.
$endgroup$
– Voltage Spike
Jul 30 at 3:05
add a comment |
$begingroup$
Putting aside the signal-processing challenges, let’s examine some noise floors.
A 62 ohm resistor produces 1 nanovolt/rtHz RMS noise at 290 Kelvin, and ignoring various crystal-flaw contributors, some of which are current-level dependent and may boost that nanovolt by orders of magnitude.
So we have a 1 nanovolt random noise floor, in a 1 volt input full scale range. If you constrain the effective-noise-bandwidth to 1 cycle-per-second.
This gives us 9 decimal digits, or 30 bits (or with sign, 31 bits).
How much input signal power must we have?
Using Vnoise_cap = sqrt(K * T / C), we learn a 10 pF capacitor at 290 degrees Kelvin will produce 20 microvolts RMS random noise.
We need to reduce the noise floor by a factor of 20,000.
This requires a capacitor of size 10 pF * 20,000 * 20,000 = 4,000 * 1,000 * 1,000 pF.
Or 4 millifarads.
What sensor energy does this require?
Power = frequency * capacitance * voltage^2
Sensor power = 1 * 0.004 farad * 1 volt^2
Sensor power = 0.004 watts
What sensors produce 4 milliwatts?
Now, for fun, guess what is the effective-noise bandwidth of 62 ohms and 0.004 Farads? The -3dB corner is about 4 radians per second. Integrating from DC to infinity, you get 6.28 radians per second.
Ain't nature fun?
$endgroup$
add a comment |
$begingroup$
Aside from the matter of need and accuracy from what I understand, there are two other issues: Leakage and noise.
If you go to high voltages (e.g., measuring 100 volts to 9.5 digits) you run into leakage issues: the voltage causes tiny currents to flow between lots of different points (e.g., between the positive and negative terminal cables in a coaxial cable, inside the switches of the meter, etc), which makes your last digit not that useful compared to an 8.5 digit meter already out there.
But when you go to lower voltages, say 1 volt, you run into noise and thermal offset issues. The last digit on 1 volt would be 1 nanovolt. Given the input impedance you would want (as even the smallest loading will have effect at 9.5 digits), you need incredibly long measurement times to get rid of thermal noise. At that point, 1/f noise really comes into the picture and makes everything even worse. And as if it wasn't even enough: thermal voltages (voltage generated between two metals when there is a temperature gradient across them) can be on the order of microvolts!
So all of these things require incredible control to get around, beyond what is realistically possible in a lab (In fact, to get the true performance out of a 6.5 digit meter at the lower ranges you already need to take things like thermal EMF and leakage into account), unless you are doing extreme calibration. And in those cases, the absolute reference labs will usually use custom Josephson-junction based references, where cryogenic temperatures and quantum-physics are used to turn a measurement of time (frequency, really) into a measurement of voltage. These can cost many hunderds of thousands of dollars and require a lot of expertise to operate.
$endgroup$
add a comment |
$begingroup$
Probably, there is a need for it, but not a big need. Not many people need that much accuracy, only some high end companies who probably make machines having also that much accuracy (for the parts that need to be measured with a 9.5 digit DMM). However, I can imagine there is a 'need' for it, or at least a wish.
The reason why there are none, is that it is probably very expensive to make one with that accuracy; if it is possible at all, it is too costly and nobody will buy it.
An analogy is a well known wafer stepper company which makes machines on nm accuracy. These machines are heavily depending on the quality of optical lenses. There are very few companies on this world who can make good lenses, and this wafer stepper company would like to have better lenses, but just at the cost that they can earn it back from customers.
$endgroup$
$begingroup$
Wafer stepper overlay accuracy must be below nanometers by now, no? Whether it's 10's or 100's of picometers, though, I'm not sure.
$endgroup$
– The Photon
Jul 28 at 0:10
$begingroup$
@ThePhoton True indeed, overlay (which is the smallest accuracy for placing layers is in 0.5 nm now afaik, maybe even smaller), however internally for some steps picometers might be used.
$endgroup$
– Michel Keijzers
Jul 28 at 0:20
$begingroup$
Also, if you have to measure or encode such precise values in an analog fashion, you'll try very hard to take them to the time instead of voltage domain ASAP.
$endgroup$
– rackandboneman
Jul 29 at 3:11
$begingroup$
I don't see how this comparison is relevant. Mechanical positioning can be measured optically, and all you need is a relative offsets to be less than 0.1 nm when performing triple patterning. But you really don't care where exactly on that big 300 mm silicon wafer you end up.
$endgroup$
– MSalters
Jul 29 at 10:05
1
$begingroup$
@MSalters Not of the new layer needs to be on top of the existing layer.
$endgroup$
– Michel Keijzers
Jul 29 at 11:20
|
show 2 more comments
$begingroup$
In a previous project I worked on, we built, tested and used precision voltage sources for Penning trap experiments. We needed $100,textV$ sources to be stable (i.e. precise, not accurate) in the sub-$mutextV$ range.
One problem with 8.5 digit multimeters and measurements at that level is that you have to deal with thermal potentials and contact potentials, which severely degrade your accuracy. Also, both effects are usually temperature dependent, which degrades your precision, unless you have good thermal stability of the test setup. If you had a 9.5 digit multimeter, you would have to have even better control over the measurement environment.
If you really, really need a 9.5 digit multimeter, current ADC technology is not sufficient. I suppose you could set up cryogenic Penning trap for that purpose. It would have to be custom-built, cost a few hundred thousand dollars and one to two PhD students. But it can be done! Calibration would be the most tricky part, but can be done against a Josephson junction array (primary standard).
$endgroup$
add a comment |
Your Answer
StackExchange.ifUsing("editor", function ()
return StackExchange.using("schematics", function ()
StackExchange.schematics.init();
);
, "cicuitlab");
StackExchange.ready(function()
var channelOptions =
tags: "".split(" "),
id: "135"
;
initTagRenderer("".split(" "), "".split(" "), channelOptions);
StackExchange.using("externalEditor", function()
// Have to fire editor after snippets, if snippets enabled
if (StackExchange.settings.snippets.snippetsEnabled)
StackExchange.using("snippets", function()
createEditor();
);
else
createEditor();
);
function createEditor()
StackExchange.prepareEditor(
heartbeatType: 'answer',
autoActivateHeartbeat: false,
convertImagesToLinks: false,
noModals: true,
showLowRepImageUploadWarning: true,
reputationToPostImages: null,
bindNavPrevention: true,
postfix: "",
imageUploader:
brandingHtml: "Powered by u003ca class="icon-imgur-white" href="https://imgur.com/"u003eu003c/au003e",
contentPolicyHtml: "User contributions licensed under u003ca href="https://creativecommons.org/licenses/by-sa/3.0/"u003ecc by-sa 3.0 with attribution requiredu003c/au003e u003ca href="https://stackoverflow.com/legal/content-policy"u003e(content policy)u003c/au003e",
allowUrls: true
,
onDemand: true,
discardSelector: ".discard-answer"
,immediatelyShowMarkdownHelp:true
);
);
Sign up or log in
StackExchange.ready(function ()
StackExchange.helpers.onClickDraftSave('#login-link');
);
Sign up using Google
Sign up using Facebook
Sign up using Email and Password
Post as a guest
Required, but never shown
StackExchange.ready(
function ()
StackExchange.openid.initPostLogin('.new-post-login', 'https%3a%2f%2felectronics.stackexchange.com%2fquestions%2f450454%2fwhy-isnt-there-any-9-5-digit-multimeter-or-higher%23new-answer', 'question_page');
);
Post as a guest
Required, but never shown
5 Answers
5
active
oldest
votes
5 Answers
5
active
oldest
votes
active
oldest
votes
active
oldest
votes
$begingroup$
Four reasons:
- Because modern meters have an autoranging function.
- Because the dynamic range of the analog system would not support 91⁄2 digits, with a range of 1 V the noise floor would be in the nanovolts (you can't get lower than nanovolts because of thermal noise, without significant cooling of what your measuring to reduce the thermal noise temperature), and all of the digits below the 9th would be noisy.
- ADCs usually have a 5 V range, and even with a 24-bit ADC, you'll have roughly 60 nV per bit which restricts the resolution of the last digits.
- On a 6.5 digit meters that are commonly used, for most measurements around a normal lab have noise in the uV range. And the last digits are commonly noisy on a 6.5 digit meter. One more digit might be nice for some applications, 3 more digits would be frivolous.
Even nanovolt meters don't have 91⁄2 digits.
For most measurements 6 (or so) digits will suffice because great care must be taken to lower the noise floor below 1 μV.
Here is a cool scale that also illustrates the point:
Source: Understanding and Applying Voltage References
It's difficult to obtain gains larger than 140dB with an analog subsystem, and about that point your also limited on resolution. Gaining doesn't help because of the noise inherent in all analog electronics, you gain up the signal, you also gain up the noise.
The marketing departments can ask for more digits, but it's not going to help engineers.
$endgroup$
9
$begingroup$
Autoranging with relays can play havoc with sensitive experiments, so in the physics lab I work in we normally turn it off. Thus for one experiment we need a 6.5 digit multimeter to get 3.5 digits at the start and not saturate the photodiode at the end.
$endgroup$
– Chris H
Jul 28 at 18:20
$begingroup$
You can take your signal, filter it, then amplify it with a gain of 2 or more, and measure three digits there (then divide by your gain for your measurement). This is usually what is done when you need more precision with a 10-bits ADC (like the one you find on most microcontrollers) for pretty much a couple of cents in parts.
$endgroup$
– Drunken Code Monkey
Jul 30 at 2:58
2
$begingroup$
@DrunkenCodeMonkey Yes, this works for 10-bits, 10bits is equivalent to 3.5digits. There is no way to increase the SNR for the frequency's you are measuring. Filtering will reduce the overall pk-pk noise, but will do nothing for sensor noise. If the noise per given frequency is 10nv/Hz at the input then there is no amount of gaining or filtering to get better SNR. The other problem is every time you add a filter or analog stage, you increase the noise.
$endgroup$
– Voltage Spike
Jul 30 at 3:05
add a comment |
$begingroup$
Four reasons:
- Because modern meters have an autoranging function.
- Because the dynamic range of the analog system would not support 91⁄2 digits, with a range of 1 V the noise floor would be in the nanovolts (you can't get lower than nanovolts because of thermal noise, without significant cooling of what your measuring to reduce the thermal noise temperature), and all of the digits below the 9th would be noisy.
- ADCs usually have a 5 V range, and even with a 24-bit ADC, you'll have roughly 60 nV per bit which restricts the resolution of the last digits.
- On a 6.5 digit meters that are commonly used, for most measurements around a normal lab have noise in the uV range. And the last digits are commonly noisy on a 6.5 digit meter. One more digit might be nice for some applications, 3 more digits would be frivolous.
Even nanovolt meters don't have 91⁄2 digits.
For most measurements 6 (or so) digits will suffice because great care must be taken to lower the noise floor below 1 μV.
Here is a cool scale that also illustrates the point:
Source: Understanding and Applying Voltage References
It's difficult to obtain gains larger than 140dB with an analog subsystem, and about that point your also limited on resolution. Gaining doesn't help because of the noise inherent in all analog electronics, you gain up the signal, you also gain up the noise.
The marketing departments can ask for more digits, but it's not going to help engineers.
$endgroup$
9
$begingroup$
Autoranging with relays can play havoc with sensitive experiments, so in the physics lab I work in we normally turn it off. Thus for one experiment we need a 6.5 digit multimeter to get 3.5 digits at the start and not saturate the photodiode at the end.
$endgroup$
– Chris H
Jul 28 at 18:20
$begingroup$
You can take your signal, filter it, then amplify it with a gain of 2 or more, and measure three digits there (then divide by your gain for your measurement). This is usually what is done when you need more precision with a 10-bits ADC (like the one you find on most microcontrollers) for pretty much a couple of cents in parts.
$endgroup$
– Drunken Code Monkey
Jul 30 at 2:58
2
$begingroup$
@DrunkenCodeMonkey Yes, this works for 10-bits, 10bits is equivalent to 3.5digits. There is no way to increase the SNR for the frequency's you are measuring. Filtering will reduce the overall pk-pk noise, but will do nothing for sensor noise. If the noise per given frequency is 10nv/Hz at the input then there is no amount of gaining or filtering to get better SNR. The other problem is every time you add a filter or analog stage, you increase the noise.
$endgroup$
– Voltage Spike
Jul 30 at 3:05
add a comment |
$begingroup$
Four reasons:
- Because modern meters have an autoranging function.
- Because the dynamic range of the analog system would not support 91⁄2 digits, with a range of 1 V the noise floor would be in the nanovolts (you can't get lower than nanovolts because of thermal noise, without significant cooling of what your measuring to reduce the thermal noise temperature), and all of the digits below the 9th would be noisy.
- ADCs usually have a 5 V range, and even with a 24-bit ADC, you'll have roughly 60 nV per bit which restricts the resolution of the last digits.
- On a 6.5 digit meters that are commonly used, for most measurements around a normal lab have noise in the uV range. And the last digits are commonly noisy on a 6.5 digit meter. One more digit might be nice for some applications, 3 more digits would be frivolous.
Even nanovolt meters don't have 91⁄2 digits.
For most measurements 6 (or so) digits will suffice because great care must be taken to lower the noise floor below 1 μV.
Here is a cool scale that also illustrates the point:
Source: Understanding and Applying Voltage References
It's difficult to obtain gains larger than 140dB with an analog subsystem, and about that point your also limited on resolution. Gaining doesn't help because of the noise inherent in all analog electronics, you gain up the signal, you also gain up the noise.
The marketing departments can ask for more digits, but it's not going to help engineers.
$endgroup$
Four reasons:
- Because modern meters have an autoranging function.
- Because the dynamic range of the analog system would not support 91⁄2 digits, with a range of 1 V the noise floor would be in the nanovolts (you can't get lower than nanovolts because of thermal noise, without significant cooling of what your measuring to reduce the thermal noise temperature), and all of the digits below the 9th would be noisy.
- ADCs usually have a 5 V range, and even with a 24-bit ADC, you'll have roughly 60 nV per bit which restricts the resolution of the last digits.
- On a 6.5 digit meters that are commonly used, for most measurements around a normal lab have noise in the uV range. And the last digits are commonly noisy on a 6.5 digit meter. One more digit might be nice for some applications, 3 more digits would be frivolous.
Even nanovolt meters don't have 91⁄2 digits.
For most measurements 6 (or so) digits will suffice because great care must be taken to lower the noise floor below 1 μV.
Here is a cool scale that also illustrates the point:
Source: Understanding and Applying Voltage References
It's difficult to obtain gains larger than 140dB with an analog subsystem, and about that point your also limited on resolution. Gaining doesn't help because of the noise inherent in all analog electronics, you gain up the signal, you also gain up the noise.
The marketing departments can ask for more digits, but it's not going to help engineers.
edited Jul 30 at 20:19
answered Jul 28 at 4:02


Voltage SpikeVoltage Spike
35.8k12 gold badges41 silver badges103 bronze badges
35.8k12 gold badges41 silver badges103 bronze badges
9
$begingroup$
Autoranging with relays can play havoc with sensitive experiments, so in the physics lab I work in we normally turn it off. Thus for one experiment we need a 6.5 digit multimeter to get 3.5 digits at the start and not saturate the photodiode at the end.
$endgroup$
– Chris H
Jul 28 at 18:20
$begingroup$
You can take your signal, filter it, then amplify it with a gain of 2 or more, and measure three digits there (then divide by your gain for your measurement). This is usually what is done when you need more precision with a 10-bits ADC (like the one you find on most microcontrollers) for pretty much a couple of cents in parts.
$endgroup$
– Drunken Code Monkey
Jul 30 at 2:58
2
$begingroup$
@DrunkenCodeMonkey Yes, this works for 10-bits, 10bits is equivalent to 3.5digits. There is no way to increase the SNR for the frequency's you are measuring. Filtering will reduce the overall pk-pk noise, but will do nothing for sensor noise. If the noise per given frequency is 10nv/Hz at the input then there is no amount of gaining or filtering to get better SNR. The other problem is every time you add a filter or analog stage, you increase the noise.
$endgroup$
– Voltage Spike
Jul 30 at 3:05
add a comment |
9
$begingroup$
Autoranging with relays can play havoc with sensitive experiments, so in the physics lab I work in we normally turn it off. Thus for one experiment we need a 6.5 digit multimeter to get 3.5 digits at the start and not saturate the photodiode at the end.
$endgroup$
– Chris H
Jul 28 at 18:20
$begingroup$
You can take your signal, filter it, then amplify it with a gain of 2 or more, and measure three digits there (then divide by your gain for your measurement). This is usually what is done when you need more precision with a 10-bits ADC (like the one you find on most microcontrollers) for pretty much a couple of cents in parts.
$endgroup$
– Drunken Code Monkey
Jul 30 at 2:58
2
$begingroup$
@DrunkenCodeMonkey Yes, this works for 10-bits, 10bits is equivalent to 3.5digits. There is no way to increase the SNR for the frequency's you are measuring. Filtering will reduce the overall pk-pk noise, but will do nothing for sensor noise. If the noise per given frequency is 10nv/Hz at the input then there is no amount of gaining or filtering to get better SNR. The other problem is every time you add a filter or analog stage, you increase the noise.
$endgroup$
– Voltage Spike
Jul 30 at 3:05
9
9
$begingroup$
Autoranging with relays can play havoc with sensitive experiments, so in the physics lab I work in we normally turn it off. Thus for one experiment we need a 6.5 digit multimeter to get 3.5 digits at the start and not saturate the photodiode at the end.
$endgroup$
– Chris H
Jul 28 at 18:20
$begingroup$
Autoranging with relays can play havoc with sensitive experiments, so in the physics lab I work in we normally turn it off. Thus for one experiment we need a 6.5 digit multimeter to get 3.5 digits at the start and not saturate the photodiode at the end.
$endgroup$
– Chris H
Jul 28 at 18:20
$begingroup$
You can take your signal, filter it, then amplify it with a gain of 2 or more, and measure three digits there (then divide by your gain for your measurement). This is usually what is done when you need more precision with a 10-bits ADC (like the one you find on most microcontrollers) for pretty much a couple of cents in parts.
$endgroup$
– Drunken Code Monkey
Jul 30 at 2:58
$begingroup$
You can take your signal, filter it, then amplify it with a gain of 2 or more, and measure three digits there (then divide by your gain for your measurement). This is usually what is done when you need more precision with a 10-bits ADC (like the one you find on most microcontrollers) for pretty much a couple of cents in parts.
$endgroup$
– Drunken Code Monkey
Jul 30 at 2:58
2
2
$begingroup$
@DrunkenCodeMonkey Yes, this works for 10-bits, 10bits is equivalent to 3.5digits. There is no way to increase the SNR for the frequency's you are measuring. Filtering will reduce the overall pk-pk noise, but will do nothing for sensor noise. If the noise per given frequency is 10nv/Hz at the input then there is no amount of gaining or filtering to get better SNR. The other problem is every time you add a filter or analog stage, you increase the noise.
$endgroup$
– Voltage Spike
Jul 30 at 3:05
$begingroup$
@DrunkenCodeMonkey Yes, this works for 10-bits, 10bits is equivalent to 3.5digits. There is no way to increase the SNR for the frequency's you are measuring. Filtering will reduce the overall pk-pk noise, but will do nothing for sensor noise. If the noise per given frequency is 10nv/Hz at the input then there is no amount of gaining or filtering to get better SNR. The other problem is every time you add a filter or analog stage, you increase the noise.
$endgroup$
– Voltage Spike
Jul 30 at 3:05
add a comment |
$begingroup$
Putting aside the signal-processing challenges, let’s examine some noise floors.
A 62 ohm resistor produces 1 nanovolt/rtHz RMS noise at 290 Kelvin, and ignoring various crystal-flaw contributors, some of which are current-level dependent and may boost that nanovolt by orders of magnitude.
So we have a 1 nanovolt random noise floor, in a 1 volt input full scale range. If you constrain the effective-noise-bandwidth to 1 cycle-per-second.
This gives us 9 decimal digits, or 30 bits (or with sign, 31 bits).
How much input signal power must we have?
Using Vnoise_cap = sqrt(K * T / C), we learn a 10 pF capacitor at 290 degrees Kelvin will produce 20 microvolts RMS random noise.
We need to reduce the noise floor by a factor of 20,000.
This requires a capacitor of size 10 pF * 20,000 * 20,000 = 4,000 * 1,000 * 1,000 pF.
Or 4 millifarads.
What sensor energy does this require?
Power = frequency * capacitance * voltage^2
Sensor power = 1 * 0.004 farad * 1 volt^2
Sensor power = 0.004 watts
What sensors produce 4 milliwatts?
Now, for fun, guess what is the effective-noise bandwidth of 62 ohms and 0.004 Farads? The -3dB corner is about 4 radians per second. Integrating from DC to infinity, you get 6.28 radians per second.
Ain't nature fun?
$endgroup$
add a comment |
$begingroup$
Putting aside the signal-processing challenges, let’s examine some noise floors.
A 62 ohm resistor produces 1 nanovolt/rtHz RMS noise at 290 Kelvin, and ignoring various crystal-flaw contributors, some of which are current-level dependent and may boost that nanovolt by orders of magnitude.
So we have a 1 nanovolt random noise floor, in a 1 volt input full scale range. If you constrain the effective-noise-bandwidth to 1 cycle-per-second.
This gives us 9 decimal digits, or 30 bits (or with sign, 31 bits).
How much input signal power must we have?
Using Vnoise_cap = sqrt(K * T / C), we learn a 10 pF capacitor at 290 degrees Kelvin will produce 20 microvolts RMS random noise.
We need to reduce the noise floor by a factor of 20,000.
This requires a capacitor of size 10 pF * 20,000 * 20,000 = 4,000 * 1,000 * 1,000 pF.
Or 4 millifarads.
What sensor energy does this require?
Power = frequency * capacitance * voltage^2
Sensor power = 1 * 0.004 farad * 1 volt^2
Sensor power = 0.004 watts
What sensors produce 4 milliwatts?
Now, for fun, guess what is the effective-noise bandwidth of 62 ohms and 0.004 Farads? The -3dB corner is about 4 radians per second. Integrating from DC to infinity, you get 6.28 radians per second.
Ain't nature fun?
$endgroup$
add a comment |
$begingroup$
Putting aside the signal-processing challenges, let’s examine some noise floors.
A 62 ohm resistor produces 1 nanovolt/rtHz RMS noise at 290 Kelvin, and ignoring various crystal-flaw contributors, some of which are current-level dependent and may boost that nanovolt by orders of magnitude.
So we have a 1 nanovolt random noise floor, in a 1 volt input full scale range. If you constrain the effective-noise-bandwidth to 1 cycle-per-second.
This gives us 9 decimal digits, or 30 bits (or with sign, 31 bits).
How much input signal power must we have?
Using Vnoise_cap = sqrt(K * T / C), we learn a 10 pF capacitor at 290 degrees Kelvin will produce 20 microvolts RMS random noise.
We need to reduce the noise floor by a factor of 20,000.
This requires a capacitor of size 10 pF * 20,000 * 20,000 = 4,000 * 1,000 * 1,000 pF.
Or 4 millifarads.
What sensor energy does this require?
Power = frequency * capacitance * voltage^2
Sensor power = 1 * 0.004 farad * 1 volt^2
Sensor power = 0.004 watts
What sensors produce 4 milliwatts?
Now, for fun, guess what is the effective-noise bandwidth of 62 ohms and 0.004 Farads? The -3dB corner is about 4 radians per second. Integrating from DC to infinity, you get 6.28 radians per second.
Ain't nature fun?
$endgroup$
Putting aside the signal-processing challenges, let’s examine some noise floors.
A 62 ohm resistor produces 1 nanovolt/rtHz RMS noise at 290 Kelvin, and ignoring various crystal-flaw contributors, some of which are current-level dependent and may boost that nanovolt by orders of magnitude.
So we have a 1 nanovolt random noise floor, in a 1 volt input full scale range. If you constrain the effective-noise-bandwidth to 1 cycle-per-second.
This gives us 9 decimal digits, or 30 bits (or with sign, 31 bits).
How much input signal power must we have?
Using Vnoise_cap = sqrt(K * T / C), we learn a 10 pF capacitor at 290 degrees Kelvin will produce 20 microvolts RMS random noise.
We need to reduce the noise floor by a factor of 20,000.
This requires a capacitor of size 10 pF * 20,000 * 20,000 = 4,000 * 1,000 * 1,000 pF.
Or 4 millifarads.
What sensor energy does this require?
Power = frequency * capacitance * voltage^2
Sensor power = 1 * 0.004 farad * 1 volt^2
Sensor power = 0.004 watts
What sensors produce 4 milliwatts?
Now, for fun, guess what is the effective-noise bandwidth of 62 ohms and 0.004 Farads? The -3dB corner is about 4 radians per second. Integrating from DC to infinity, you get 6.28 radians per second.
Ain't nature fun?
edited Aug 1 at 12:03
answered Jul 28 at 3:03
analogsystemsrfanalogsystemsrf
18.5k2 gold badges8 silver badges25 bronze badges
18.5k2 gold badges8 silver badges25 bronze badges
add a comment |
add a comment |
$begingroup$
Aside from the matter of need and accuracy from what I understand, there are two other issues: Leakage and noise.
If you go to high voltages (e.g., measuring 100 volts to 9.5 digits) you run into leakage issues: the voltage causes tiny currents to flow between lots of different points (e.g., between the positive and negative terminal cables in a coaxial cable, inside the switches of the meter, etc), which makes your last digit not that useful compared to an 8.5 digit meter already out there.
But when you go to lower voltages, say 1 volt, you run into noise and thermal offset issues. The last digit on 1 volt would be 1 nanovolt. Given the input impedance you would want (as even the smallest loading will have effect at 9.5 digits), you need incredibly long measurement times to get rid of thermal noise. At that point, 1/f noise really comes into the picture and makes everything even worse. And as if it wasn't even enough: thermal voltages (voltage generated between two metals when there is a temperature gradient across them) can be on the order of microvolts!
So all of these things require incredible control to get around, beyond what is realistically possible in a lab (In fact, to get the true performance out of a 6.5 digit meter at the lower ranges you already need to take things like thermal EMF and leakage into account), unless you are doing extreme calibration. And in those cases, the absolute reference labs will usually use custom Josephson-junction based references, where cryogenic temperatures and quantum-physics are used to turn a measurement of time (frequency, really) into a measurement of voltage. These can cost many hunderds of thousands of dollars and require a lot of expertise to operate.
$endgroup$
add a comment |
$begingroup$
Aside from the matter of need and accuracy from what I understand, there are two other issues: Leakage and noise.
If you go to high voltages (e.g., measuring 100 volts to 9.5 digits) you run into leakage issues: the voltage causes tiny currents to flow between lots of different points (e.g., between the positive and negative terminal cables in a coaxial cable, inside the switches of the meter, etc), which makes your last digit not that useful compared to an 8.5 digit meter already out there.
But when you go to lower voltages, say 1 volt, you run into noise and thermal offset issues. The last digit on 1 volt would be 1 nanovolt. Given the input impedance you would want (as even the smallest loading will have effect at 9.5 digits), you need incredibly long measurement times to get rid of thermal noise. At that point, 1/f noise really comes into the picture and makes everything even worse. And as if it wasn't even enough: thermal voltages (voltage generated between two metals when there is a temperature gradient across them) can be on the order of microvolts!
So all of these things require incredible control to get around, beyond what is realistically possible in a lab (In fact, to get the true performance out of a 6.5 digit meter at the lower ranges you already need to take things like thermal EMF and leakage into account), unless you are doing extreme calibration. And in those cases, the absolute reference labs will usually use custom Josephson-junction based references, where cryogenic temperatures and quantum-physics are used to turn a measurement of time (frequency, really) into a measurement of voltage. These can cost many hunderds of thousands of dollars and require a lot of expertise to operate.
$endgroup$
add a comment |
$begingroup$
Aside from the matter of need and accuracy from what I understand, there are two other issues: Leakage and noise.
If you go to high voltages (e.g., measuring 100 volts to 9.5 digits) you run into leakage issues: the voltage causes tiny currents to flow between lots of different points (e.g., between the positive and negative terminal cables in a coaxial cable, inside the switches of the meter, etc), which makes your last digit not that useful compared to an 8.5 digit meter already out there.
But when you go to lower voltages, say 1 volt, you run into noise and thermal offset issues. The last digit on 1 volt would be 1 nanovolt. Given the input impedance you would want (as even the smallest loading will have effect at 9.5 digits), you need incredibly long measurement times to get rid of thermal noise. At that point, 1/f noise really comes into the picture and makes everything even worse. And as if it wasn't even enough: thermal voltages (voltage generated between two metals when there is a temperature gradient across them) can be on the order of microvolts!
So all of these things require incredible control to get around, beyond what is realistically possible in a lab (In fact, to get the true performance out of a 6.5 digit meter at the lower ranges you already need to take things like thermal EMF and leakage into account), unless you are doing extreme calibration. And in those cases, the absolute reference labs will usually use custom Josephson-junction based references, where cryogenic temperatures and quantum-physics are used to turn a measurement of time (frequency, really) into a measurement of voltage. These can cost many hunderds of thousands of dollars and require a lot of expertise to operate.
$endgroup$
Aside from the matter of need and accuracy from what I understand, there are two other issues: Leakage and noise.
If you go to high voltages (e.g., measuring 100 volts to 9.5 digits) you run into leakage issues: the voltage causes tiny currents to flow between lots of different points (e.g., between the positive and negative terminal cables in a coaxial cable, inside the switches of the meter, etc), which makes your last digit not that useful compared to an 8.5 digit meter already out there.
But when you go to lower voltages, say 1 volt, you run into noise and thermal offset issues. The last digit on 1 volt would be 1 nanovolt. Given the input impedance you would want (as even the smallest loading will have effect at 9.5 digits), you need incredibly long measurement times to get rid of thermal noise. At that point, 1/f noise really comes into the picture and makes everything even worse. And as if it wasn't even enough: thermal voltages (voltage generated between two metals when there is a temperature gradient across them) can be on the order of microvolts!
So all of these things require incredible control to get around, beyond what is realistically possible in a lab (In fact, to get the true performance out of a 6.5 digit meter at the lower ranges you already need to take things like thermal EMF and leakage into account), unless you are doing extreme calibration. And in those cases, the absolute reference labs will usually use custom Josephson-junction based references, where cryogenic temperatures and quantum-physics are used to turn a measurement of time (frequency, really) into a measurement of voltage. These can cost many hunderds of thousands of dollars and require a lot of expertise to operate.
edited Jul 28 at 21:34


a CVn
2242 silver badges12 bronze badges
2242 silver badges12 bronze badges
answered Jul 28 at 9:23


Joren VaesJoren Vaes
8,79515 silver badges49 bronze badges
8,79515 silver badges49 bronze badges
add a comment |
add a comment |
$begingroup$
Probably, there is a need for it, but not a big need. Not many people need that much accuracy, only some high end companies who probably make machines having also that much accuracy (for the parts that need to be measured with a 9.5 digit DMM). However, I can imagine there is a 'need' for it, or at least a wish.
The reason why there are none, is that it is probably very expensive to make one with that accuracy; if it is possible at all, it is too costly and nobody will buy it.
An analogy is a well known wafer stepper company which makes machines on nm accuracy. These machines are heavily depending on the quality of optical lenses. There are very few companies on this world who can make good lenses, and this wafer stepper company would like to have better lenses, but just at the cost that they can earn it back from customers.
$endgroup$
$begingroup$
Wafer stepper overlay accuracy must be below nanometers by now, no? Whether it's 10's or 100's of picometers, though, I'm not sure.
$endgroup$
– The Photon
Jul 28 at 0:10
$begingroup$
@ThePhoton True indeed, overlay (which is the smallest accuracy for placing layers is in 0.5 nm now afaik, maybe even smaller), however internally for some steps picometers might be used.
$endgroup$
– Michel Keijzers
Jul 28 at 0:20
$begingroup$
Also, if you have to measure or encode such precise values in an analog fashion, you'll try very hard to take them to the time instead of voltage domain ASAP.
$endgroup$
– rackandboneman
Jul 29 at 3:11
$begingroup$
I don't see how this comparison is relevant. Mechanical positioning can be measured optically, and all you need is a relative offsets to be less than 0.1 nm when performing triple patterning. But you really don't care where exactly on that big 300 mm silicon wafer you end up.
$endgroup$
– MSalters
Jul 29 at 10:05
1
$begingroup$
@MSalters Not of the new layer needs to be on top of the existing layer.
$endgroup$
– Michel Keijzers
Jul 29 at 11:20
|
show 2 more comments
$begingroup$
Probably, there is a need for it, but not a big need. Not many people need that much accuracy, only some high end companies who probably make machines having also that much accuracy (for the parts that need to be measured with a 9.5 digit DMM). However, I can imagine there is a 'need' for it, or at least a wish.
The reason why there are none, is that it is probably very expensive to make one with that accuracy; if it is possible at all, it is too costly and nobody will buy it.
An analogy is a well known wafer stepper company which makes machines on nm accuracy. These machines are heavily depending on the quality of optical lenses. There are very few companies on this world who can make good lenses, and this wafer stepper company would like to have better lenses, but just at the cost that they can earn it back from customers.
$endgroup$
$begingroup$
Wafer stepper overlay accuracy must be below nanometers by now, no? Whether it's 10's or 100's of picometers, though, I'm not sure.
$endgroup$
– The Photon
Jul 28 at 0:10
$begingroup$
@ThePhoton True indeed, overlay (which is the smallest accuracy for placing layers is in 0.5 nm now afaik, maybe even smaller), however internally for some steps picometers might be used.
$endgroup$
– Michel Keijzers
Jul 28 at 0:20
$begingroup$
Also, if you have to measure or encode such precise values in an analog fashion, you'll try very hard to take them to the time instead of voltage domain ASAP.
$endgroup$
– rackandboneman
Jul 29 at 3:11
$begingroup$
I don't see how this comparison is relevant. Mechanical positioning can be measured optically, and all you need is a relative offsets to be less than 0.1 nm when performing triple patterning. But you really don't care where exactly on that big 300 mm silicon wafer you end up.
$endgroup$
– MSalters
Jul 29 at 10:05
1
$begingroup$
@MSalters Not of the new layer needs to be on top of the existing layer.
$endgroup$
– Michel Keijzers
Jul 29 at 11:20
|
show 2 more comments
$begingroup$
Probably, there is a need for it, but not a big need. Not many people need that much accuracy, only some high end companies who probably make machines having also that much accuracy (for the parts that need to be measured with a 9.5 digit DMM). However, I can imagine there is a 'need' for it, or at least a wish.
The reason why there are none, is that it is probably very expensive to make one with that accuracy; if it is possible at all, it is too costly and nobody will buy it.
An analogy is a well known wafer stepper company which makes machines on nm accuracy. These machines are heavily depending on the quality of optical lenses. There are very few companies on this world who can make good lenses, and this wafer stepper company would like to have better lenses, but just at the cost that they can earn it back from customers.
$endgroup$
Probably, there is a need for it, but not a big need. Not many people need that much accuracy, only some high end companies who probably make machines having also that much accuracy (for the parts that need to be measured with a 9.5 digit DMM). However, I can imagine there is a 'need' for it, or at least a wish.
The reason why there are none, is that it is probably very expensive to make one with that accuracy; if it is possible at all, it is too costly and nobody will buy it.
An analogy is a well known wafer stepper company which makes machines on nm accuracy. These machines are heavily depending on the quality of optical lenses. There are very few companies on this world who can make good lenses, and this wafer stepper company would like to have better lenses, but just at the cost that they can earn it back from customers.
answered Jul 27 at 22:05


Michel KeijzersMichel Keijzers
8,07010 gold badges35 silver badges78 bronze badges
8,07010 gold badges35 silver badges78 bronze badges
$begingroup$
Wafer stepper overlay accuracy must be below nanometers by now, no? Whether it's 10's or 100's of picometers, though, I'm not sure.
$endgroup$
– The Photon
Jul 28 at 0:10
$begingroup$
@ThePhoton True indeed, overlay (which is the smallest accuracy for placing layers is in 0.5 nm now afaik, maybe even smaller), however internally for some steps picometers might be used.
$endgroup$
– Michel Keijzers
Jul 28 at 0:20
$begingroup$
Also, if you have to measure or encode such precise values in an analog fashion, you'll try very hard to take them to the time instead of voltage domain ASAP.
$endgroup$
– rackandboneman
Jul 29 at 3:11
$begingroup$
I don't see how this comparison is relevant. Mechanical positioning can be measured optically, and all you need is a relative offsets to be less than 0.1 nm when performing triple patterning. But you really don't care where exactly on that big 300 mm silicon wafer you end up.
$endgroup$
– MSalters
Jul 29 at 10:05
1
$begingroup$
@MSalters Not of the new layer needs to be on top of the existing layer.
$endgroup$
– Michel Keijzers
Jul 29 at 11:20
|
show 2 more comments
$begingroup$
Wafer stepper overlay accuracy must be below nanometers by now, no? Whether it's 10's or 100's of picometers, though, I'm not sure.
$endgroup$
– The Photon
Jul 28 at 0:10
$begingroup$
@ThePhoton True indeed, overlay (which is the smallest accuracy for placing layers is in 0.5 nm now afaik, maybe even smaller), however internally for some steps picometers might be used.
$endgroup$
– Michel Keijzers
Jul 28 at 0:20
$begingroup$
Also, if you have to measure or encode such precise values in an analog fashion, you'll try very hard to take them to the time instead of voltage domain ASAP.
$endgroup$
– rackandboneman
Jul 29 at 3:11
$begingroup$
I don't see how this comparison is relevant. Mechanical positioning can be measured optically, and all you need is a relative offsets to be less than 0.1 nm when performing triple patterning. But you really don't care where exactly on that big 300 mm silicon wafer you end up.
$endgroup$
– MSalters
Jul 29 at 10:05
1
$begingroup$
@MSalters Not of the new layer needs to be on top of the existing layer.
$endgroup$
– Michel Keijzers
Jul 29 at 11:20
$begingroup$
Wafer stepper overlay accuracy must be below nanometers by now, no? Whether it's 10's or 100's of picometers, though, I'm not sure.
$endgroup$
– The Photon
Jul 28 at 0:10
$begingroup$
Wafer stepper overlay accuracy must be below nanometers by now, no? Whether it's 10's or 100's of picometers, though, I'm not sure.
$endgroup$
– The Photon
Jul 28 at 0:10
$begingroup$
@ThePhoton True indeed, overlay (which is the smallest accuracy for placing layers is in 0.5 nm now afaik, maybe even smaller), however internally for some steps picometers might be used.
$endgroup$
– Michel Keijzers
Jul 28 at 0:20
$begingroup$
@ThePhoton True indeed, overlay (which is the smallest accuracy for placing layers is in 0.5 nm now afaik, maybe even smaller), however internally for some steps picometers might be used.
$endgroup$
– Michel Keijzers
Jul 28 at 0:20
$begingroup$
Also, if you have to measure or encode such precise values in an analog fashion, you'll try very hard to take them to the time instead of voltage domain ASAP.
$endgroup$
– rackandboneman
Jul 29 at 3:11
$begingroup$
Also, if you have to measure or encode such precise values in an analog fashion, you'll try very hard to take them to the time instead of voltage domain ASAP.
$endgroup$
– rackandboneman
Jul 29 at 3:11
$begingroup$
I don't see how this comparison is relevant. Mechanical positioning can be measured optically, and all you need is a relative offsets to be less than 0.1 nm when performing triple patterning. But you really don't care where exactly on that big 300 mm silicon wafer you end up.
$endgroup$
– MSalters
Jul 29 at 10:05
$begingroup$
I don't see how this comparison is relevant. Mechanical positioning can be measured optically, and all you need is a relative offsets to be less than 0.1 nm when performing triple patterning. But you really don't care where exactly on that big 300 mm silicon wafer you end up.
$endgroup$
– MSalters
Jul 29 at 10:05
1
1
$begingroup$
@MSalters Not of the new layer needs to be on top of the existing layer.
$endgroup$
– Michel Keijzers
Jul 29 at 11:20
$begingroup$
@MSalters Not of the new layer needs to be on top of the existing layer.
$endgroup$
– Michel Keijzers
Jul 29 at 11:20
|
show 2 more comments
$begingroup$
In a previous project I worked on, we built, tested and used precision voltage sources for Penning trap experiments. We needed $100,textV$ sources to be stable (i.e. precise, not accurate) in the sub-$mutextV$ range.
One problem with 8.5 digit multimeters and measurements at that level is that you have to deal with thermal potentials and contact potentials, which severely degrade your accuracy. Also, both effects are usually temperature dependent, which degrades your precision, unless you have good thermal stability of the test setup. If you had a 9.5 digit multimeter, you would have to have even better control over the measurement environment.
If you really, really need a 9.5 digit multimeter, current ADC technology is not sufficient. I suppose you could set up cryogenic Penning trap for that purpose. It would have to be custom-built, cost a few hundred thousand dollars and one to two PhD students. But it can be done! Calibration would be the most tricky part, but can be done against a Josephson junction array (primary standard).
$endgroup$
add a comment |
$begingroup$
In a previous project I worked on, we built, tested and used precision voltage sources for Penning trap experiments. We needed $100,textV$ sources to be stable (i.e. precise, not accurate) in the sub-$mutextV$ range.
One problem with 8.5 digit multimeters and measurements at that level is that you have to deal with thermal potentials and contact potentials, which severely degrade your accuracy. Also, both effects are usually temperature dependent, which degrades your precision, unless you have good thermal stability of the test setup. If you had a 9.5 digit multimeter, you would have to have even better control over the measurement environment.
If you really, really need a 9.5 digit multimeter, current ADC technology is not sufficient. I suppose you could set up cryogenic Penning trap for that purpose. It would have to be custom-built, cost a few hundred thousand dollars and one to two PhD students. But it can be done! Calibration would be the most tricky part, but can be done against a Josephson junction array (primary standard).
$endgroup$
add a comment |
$begingroup$
In a previous project I worked on, we built, tested and used precision voltage sources for Penning trap experiments. We needed $100,textV$ sources to be stable (i.e. precise, not accurate) in the sub-$mutextV$ range.
One problem with 8.5 digit multimeters and measurements at that level is that you have to deal with thermal potentials and contact potentials, which severely degrade your accuracy. Also, both effects are usually temperature dependent, which degrades your precision, unless you have good thermal stability of the test setup. If you had a 9.5 digit multimeter, you would have to have even better control over the measurement environment.
If you really, really need a 9.5 digit multimeter, current ADC technology is not sufficient. I suppose you could set up cryogenic Penning trap for that purpose. It would have to be custom-built, cost a few hundred thousand dollars and one to two PhD students. But it can be done! Calibration would be the most tricky part, but can be done against a Josephson junction array (primary standard).
$endgroup$
In a previous project I worked on, we built, tested and used precision voltage sources for Penning trap experiments. We needed $100,textV$ sources to be stable (i.e. precise, not accurate) in the sub-$mutextV$ range.
One problem with 8.5 digit multimeters and measurements at that level is that you have to deal with thermal potentials and contact potentials, which severely degrade your accuracy. Also, both effects are usually temperature dependent, which degrades your precision, unless you have good thermal stability of the test setup. If you had a 9.5 digit multimeter, you would have to have even better control over the measurement environment.
If you really, really need a 9.5 digit multimeter, current ADC technology is not sufficient. I suppose you could set up cryogenic Penning trap for that purpose. It would have to be custom-built, cost a few hundred thousand dollars and one to two PhD students. But it can be done! Calibration would be the most tricky part, but can be done against a Josephson junction array (primary standard).
answered Jul 29 at 13:30
Martin J.H.Martin J.H.
4511 gold badge4 silver badges12 bronze badges
4511 gold badge4 silver badges12 bronze badges
add a comment |
add a comment |
Thanks for contributing an answer to Electrical Engineering Stack Exchange!
- Please be sure to answer the question. Provide details and share your research!
But avoid …
- Asking for help, clarification, or responding to other answers.
- Making statements based on opinion; back them up with references or personal experience.
Use MathJax to format equations. MathJax reference.
To learn more, see our tips on writing great answers.
Sign up or log in
StackExchange.ready(function ()
StackExchange.helpers.onClickDraftSave('#login-link');
);
Sign up using Google
Sign up using Facebook
Sign up using Email and Password
Post as a guest
Required, but never shown
StackExchange.ready(
function ()
StackExchange.openid.initPostLogin('.new-post-login', 'https%3a%2f%2felectronics.stackexchange.com%2fquestions%2f450454%2fwhy-isnt-there-any-9-5-digit-multimeter-or-higher%23new-answer', 'question_page');
);
Post as a guest
Required, but never shown
Sign up or log in
StackExchange.ready(function ()
StackExchange.helpers.onClickDraftSave('#login-link');
);
Sign up using Google
Sign up using Facebook
Sign up using Email and Password
Post as a guest
Required, but never shown
Sign up or log in
StackExchange.ready(function ()
StackExchange.helpers.onClickDraftSave('#login-link');
);
Sign up using Google
Sign up using Facebook
Sign up using Email and Password
Post as a guest
Required, but never shown
Sign up or log in
StackExchange.ready(function ()
StackExchange.helpers.onClickDraftSave('#login-link');
);
Sign up using Google
Sign up using Facebook
Sign up using Email and Password
Sign up using Google
Sign up using Facebook
Sign up using Email and Password
Post as a guest
Required, but never shown
Required, but never shown
Required, but never shown
Required, but never shown
Required, but never shown
Required, but never shown
Required, but never shown
Required, but never shown
Required, but never shown
i1sCrcN3l1epVUPeQ28DAv2RH9n OeQqEexub C
10
$begingroup$
What is your goal?
$endgroup$
– Chris Stratton
Jul 27 at 22:04
38
$begingroup$
You'd need a 10.5 digit meter to calibrate it.
$endgroup$
– Transistor
Jul 27 at 22:09
11
$begingroup$
What's the true accuracy of even that 8.5 digit DMM? Probably not 1 part in 100 million...
$endgroup$
– Brian Drummond
Jul 27 at 23:03
12
$begingroup$
Check NIST. I think you'll find that accuracy of their best Josephson Junction devices is on the order of a some parts in $10^10$. So, roughly speaking, about 9.5 digits. And that's under optimal conditions. The equipment used to provide such a standard costs about $300k each and will probably require a PhD to operate well. There's a recent 2018 paper on the topic, "Impact of the latest generation of Josephson voltage standards in ac and dc electric metrology" by Rüfenacht, et al. DOI: 10.1088/1681-7575/aad41a. You can buy a voltage standard that is 9.5 digits. Not a multimeter, though.
$endgroup$
– jonk
Jul 28 at 0:46
7
$begingroup$
Every potential customer must answer for themselves the following questions: What are you trying to measure? Why do you require or want an accuracy of around a part in 1000 million? How would you calibrate it? What is your budget?
$endgroup$
– Russell McMahon
Jul 28 at 2:54